NTS realiza a Gaseificação do novo Ponto de Entrega de Cubatão II
Após a gaseificação e início da operação do ponto de entrega e recebimento RPBC, a NTS preparou o novo Ponto de Entrega (PE) de Cubatão II para sua gaseificação. As ações foram discutidas pelo time de campo e escritório, e com nossa cliente Petrobras.
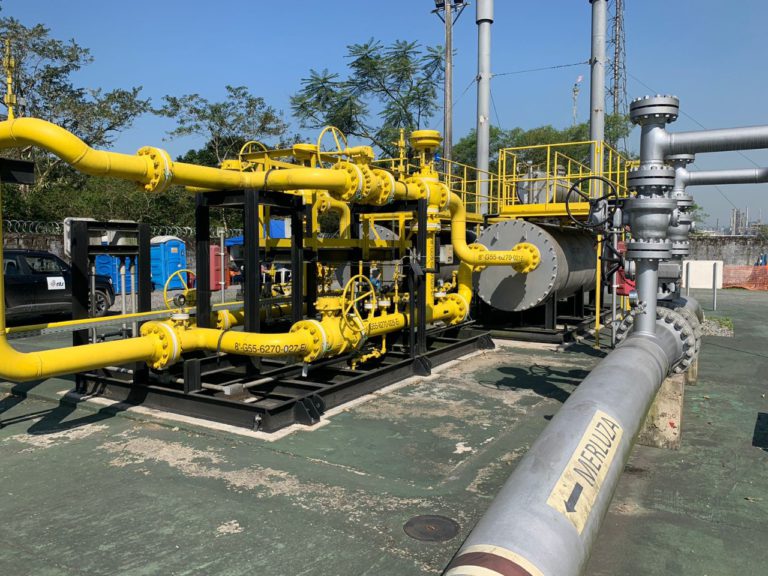
Após a gaseificação e início da operação do ponto de entrega e recebimento RPBC, a NTS preparou o novo Ponto de Entrega (PE) de Cubatão II para sua gaseificação. As ações foram discutidas pelo time de campo e escritório, e com nossa cliente Petrobras.
Mas afinal, você sabe no que consiste esta preparação? Convidamos o time responsável para apresentar as etapas que antecedem o início da operação de um Ponto de Entrega. Veja o que eles têm a dizer:
O primeiro passo consistiu no planejamento: estabelecer objetivos, prever e neutralizar efeitos indesejáveis antes que se materializem. Para isso, foi necessária e fundamental a participação de todos(as) os(as) envolvidos(as), através de comentários, sugestões e informações”. “Um procedimento é antes de tudo uma ferramenta dinâmica, que deve ser aperfeiçoada até as vésperas da sua utilização, eliminando-se lacunas”., informou Homero Ancilloti, Consultor de Gasodutos.
Para o Consultor em Gasodutos Rubens Stafin é importante tornar o trabalho ágil e seguro. “Realizamos planejamento detalhado observando o PONR, para abranger o maior número de possíveis problemas e interferências que possam ser encontradas. Da mesma forma que definir a sequência, mensurando o tempo para cada tarefa a fim de ter um controle mais aprimorado. E antes de iniciar as atividades, realizar checagem das ferramentas e sobressalentes necessários.”.
Após as etapas de planejamento, o time pode enfim iniciar as atividades operacionais de campo, passo a passo, conforme relatos abaixo:
Segundo Márcio Azevedo, Técnico de Gasodutos, uma etapa primordial foi a realização do teste funcional da lógica do CLP, como também os testes de comunicação entre o CLP x Computadores de Vazão x Cromatógrafo e sistema Supervisório do CCO, para o atendimento do comissionamento, de forma a garantir que toda a comunicação estará operacional para o monitoramento remoto da estação.
“Foi realizado também a verificação de funcionamento e calibração de todos os transmissores de pressão e temperatura, assim como dos manômetros, termômetros e pressostatos presentes na estação. Tornando as indicações das variáveis mais precisas e confiáveis para o Centro de Controle Operacional – CCO e ao Operador(a) em campo.”, ressaltou João Azevedo, Técnico de Gasodutos.
“Ainda durante a fase de testes da estação para início operacional, foi efetuado uma inspeção interna, conforme a NR-13, pelas equipes de Integridade e Operação. No procedimento foi observado resíduos (fuligem de oxidação) nos interiores dos filtros e realizada a limpeza interna para garantia da integridade da qualidade de entrega do gás natural para nosso importante cliente.”, explicou Amarildo Silva, Técnico de Gasoduto.
Para o Técnico de Gasodutos Anderson Panzica, o maior desafio encontrado foi a realização do comissionamento e do teste funcional do sistema de aquecimento do gás, que evita a formação de gelo na tubulação e nos equipamentos. “Realizamos a limpeza total do equipamento, drenagem e substituição da água, testes das válvulas reguladoras, válvulas de segurança e toda a automação que envolve este importante equipamento para o ponto de entrega”.
O sistema de redução de pressão, que consiste no item mais sensível da instalação, necessitou do envolvimento de todos, não somente por ser o item de maior risco, mas também para que todos conheçam os novos equipamentos a serem operados pela NTS, de forma a estarem preparados para uma possível manutenção, seja ela preventiva ou corretiva a qualquer hora do dia ou da noite.
Em resumo, João Bregalda, Técnico Programador da base de Mauá, concluiu das seguinte maneira as atividades realizadas: “Comissionar um novo Ponto de Entrega é um desafio enorme, que exige muito preparo, testes, organização e recursos. Em Cubatão II, assim como no comissionamento do PE/PR RPBC, dedicamos muitas horas da nossa equipe de São Vicente com testes, calibrações, levantamentos e correções. Envolvemos a equipe de Mauá e diversas equipes terceirizadas, adquirimos materiais e, em muitas vezes tivemos atividades distintas acontecendo em paralelo. O trabalho em equipe foi primordial para que tivéssemos sintonia e tranquilidade, passando pelos contratempos com foco em nosso objetivo: comissionar sem acidentes.”